SenSLM - Contrôler les pièces fabriquées par impression 3D
Ingénierie et Architecture Projets de recherche appliquée et développement Valais
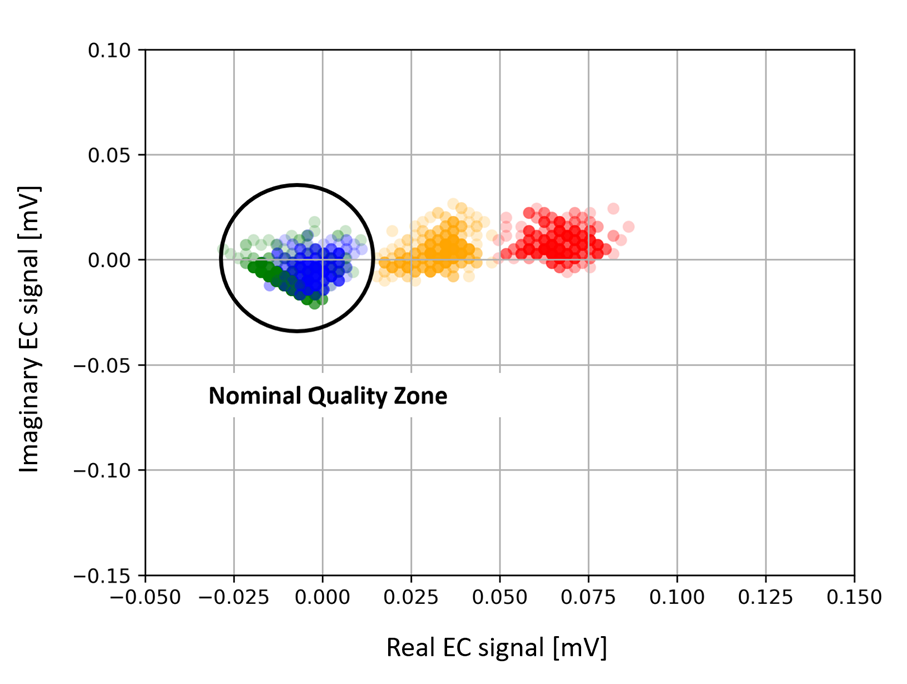
L'intérêt pour la technologie de l'impression 3D s'étend désormais au-delà du prototypage et de la personnalisation, avec de nombreuses applications dans l'aéronautique, le MedTech, l'automobile, l'horlogerie ou l'industrie des machines. Si l'impression 3D ne va pas remplacer l'usinage ou l'injection en ce qui concerne la production de masse, ses atouts se révèlent intéressants pour des productions personnalisées ou allant jusqu'à 1'000 pièces. Les secteurs susmentionnés souhaitent profiter de la liberté de géométrie et de la réduction du "time to market" permis pour la fabrication additive. Leur but est donc d'intégrer des composants produits par cette technologie à des produits commerciaux. Mais, comme dans le cas des méthodes de fabrication traditionnelles, cela requiert que les pièces respectent les normes de qualité. Car, malgré la grande précision du procédé, les pièces fabriquées par impression 3D sont susceptibles de contenir des défauts, comme de la porosité ou des fissures. Cela peut se produire notamment lorsque les paramètres d'impression ne sont pas adaptés au matériau ou à la géométrie de la pièce.
La présence de défaut doit alors être détectée, de même que les propriétés comparées à une norme permettant l'acceptation ou le rejet de la pièce. Cela est permis grâce à l'application de contrôles non invasifs et structurés selon des normes, appelées "contrôles non destructifs normalisés". Jusqu'à présent, dans le cas de la fabrication additive, les contrôles non destructifs étaient habituellement réalisés après l'impression de la pièce. Ce contrôle postproduction rallonge le processus et génère des coûts inutiles pour la finition ou l'éventuelle élimination de pièces défectueuses. Le délai entre l'impression et le contrôle ne permet pas de corriger immédiatement les éventuelles dérives du procédé liées, par exemple, à une variation de la qualité entre les lots de poudres, au dysfonctionnement d'une imprimante ou simplement à l'impression d'une géométrie différente. Ce manque de réactivité désavantage les producteurs qui souhaitent précisément profiter de la flexibilité de l'impression 3D.
C'est pour remédier à ces problèmes que la spin-off AMiquam, basée à Gland, a développé un capteur innovant capable de réaliser les contrôles requis par les normes directement durant le processus d'impression. Alors que son capteur se trouve dans la dernière étape avant sa mise sur le marché, elle collabore avec l'Institut Systèmes industriels de la HEI dans le cadre du projet SenSLM, pour une ultime phase de test. Les chercheur-es vérifient ainsi que le capteur ait correctement détecté les défauts d'une pièce ou n'en ait pas omis. Cette collaboration permet à AMiquam de bénéficier des machines, ainsi que des compétences pointues en matériaux de l'équipe de recherche. De son côté, cette dernière dispose d'un outil de contrôle inédit, grâce auquel elle peut tester des assemblages de matériaux innovants.
Un appel à projets destiné aux entreprises impactées par la crise sanitaire
Le projet décrit ci-dessus fait partie d'un appel à projets extraordinaire intitulé "Après Covid-19". Il a été lancé en juillet 2020 par le Conseil de domaine Ingénierie et Architecture de la HES-SO. Ces fonds sont destinés aux professeur-es proches des sociétés de services et d'entreprises suisses impactées par la crise sanitaire. Les hautes écoles concernées par cet appel à projets sont :
- HE-Arc Ingénierie ;
- Haute école d'ingénierie et d'architecture de Fribourg - HEIA-FR ;
- Haute école du paysage, d'ingénierie et d'architecture de Genève (HEPIA) ;
- HES-SO Valais/Wallis - Haute Ecole d'Ingénierie - HEI ;
- Haute Ecole d'Ingénierie et de Gestion du Canton de Vaud - HEIG-VD ;
- CHANGINS - Haute école de viticulture et œnologie.