ArCoBio - Alliage métallique d'argent composite biosourcé
Ingénierie et Architecture
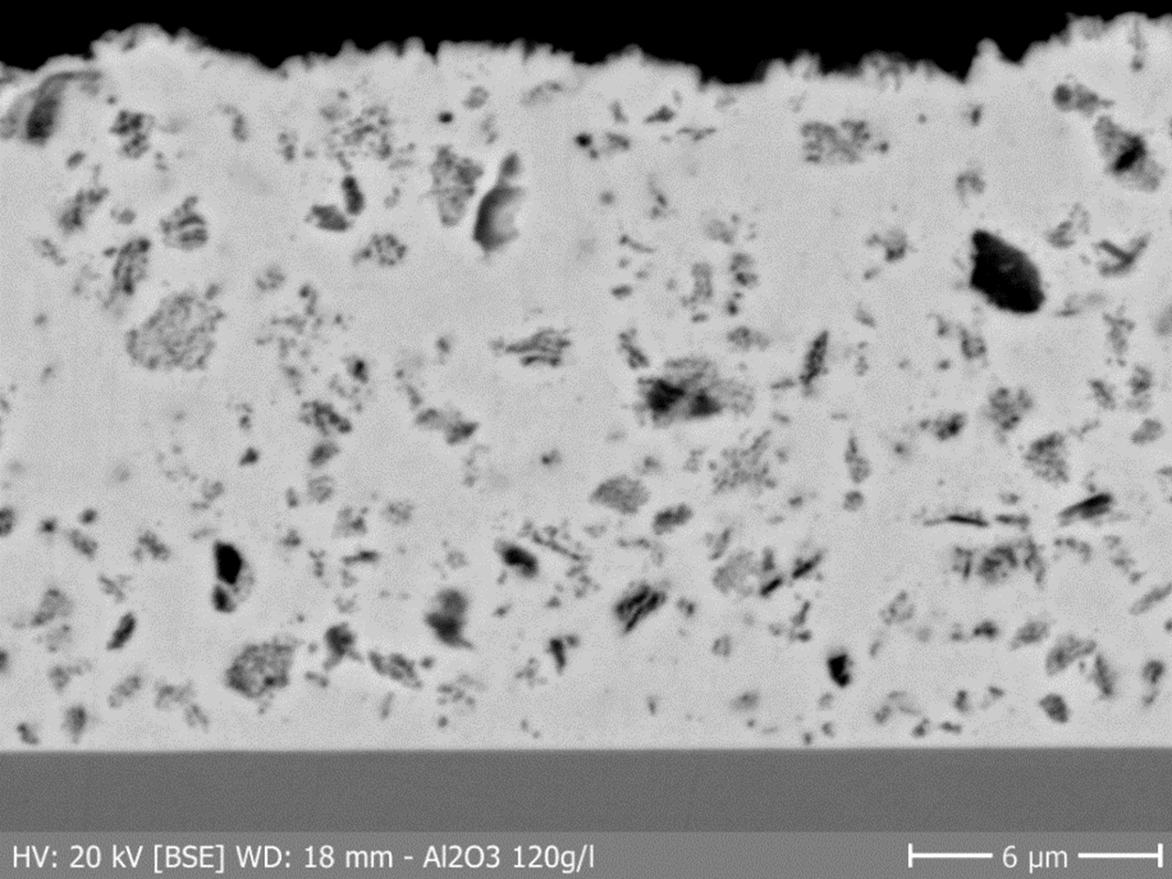
Le but du projet est d’améliorer les propriétés mécaniques et tribologiques de ces métaux sans baisser leur conductibilité par des changements microstructuraux résultant de leur mariage avec des nanoparticules, en particulier venant de synthèses vertes ou biosourcées.
La voie classique
Le dépôt de couches métalliques composites contenant des microparticules est réalisé par voie électrochimique.
Dans le domaine de l’injection plastique, des couches composites Ni-PTFE sont couramment utilisées. La présence des particules de PTFE abaisse notablement le coefficient de frottement et augmente la résistance à l’usure des moules. Cependant, dans le cas de la connectique, ceci augmenterait considérablement la résistivité électrique. Dans l’outillage ou de l’automobile, des couches composites à base de Ni ou de Cr alliées avec des particules dures. Ces revêtements présentent d’excellentes propriétés anti-usure, néanmoins l’aspect de surface est très hétérogène suite à la coalition d’amas de particules au sein du revêtement.
Les défis résultent dans la taille des particules, de leur aptitude à être mises en dispersion et des liens qu’elles peuvent établir une fois incorporées avec la matrice métallique et dont dépendront les propriétés mécaniques et tribologiques. Mécaniquement, un tel système biphasé macroscopique présente le compromis entre les propriétés de chacune des phases, les particules et la matrice métallique. Ainsi, par exemple, la phase la plus ductile dictera la déformation plastique du composite.
Pour dépasser ce compromis, il a été tenté d’incorporer des nanoparticules sous forme de poudre sèche dispersées dans un électrolyte. Deux faits péjorent cette approche :
- Les nanoparticules forment des « clusters » lors du séchage, leur taille moyenne devient telle que cela revient à une incorporation classique de type composite.
- Les manipulations de nanoparticules sèches sont potentiellement dangereuses et la toxicité en est peu connue.
L’innovation
Le projet consiste à produire les nanoparticules et à les incorporer dans le revêtement métallique par voie électrochimique. Il repose sur 2 compétences-clé :
- La capacité de synthétiser des nanoparticules biosourcées en milieu liquide (HEPIA).
- La capacité de formuler un bain chimique comportant la solution d’ions argent chargée de nanoparticules (HE-Arc Ingénierie)
Le procédé de co-déposition produit un revêtement nano-composite dans lequel les interactions à l’échelle atomique dictent le comportement mécanique macroscopique. L’amélioration des propriétés mécaniques résulterait du durcissement structural. Ce type de nanomatériaux est impossible à produire par la voie classique (coulée).
Dans ce projet, les revêtements électrochimiques en argent comportant des nanoparticules sont explorés d’un point de vue mécanique et plus particulièrement leur résistance à l’usure. L’argent est choisi pour sa haute ductilité et conductivité électrique. Le champ d’application s’étend des contacts électriques frottant à l’horlogerie. Les résultats de ce projet sont très prometteurs puisque :
- L’utilisation de nano-particules de type dioxyde de titane permet de réaliser des revêtements composites de type Ag-TiO2. Avec une concentration de 30 g/l de nano-particules, l’usure des revêtements peut être améliorées de 40 %.
- Dans le cas de nano-composites élaborés avec du dioxyde de zirconium, on note une amélioration drastique de la résistance à l’usure de plus de 60 % pour une concentration en nano-particules de 30 g/l de ZrO2.
Il est important d’approfondir la recherche dans ce procédé afin d’atteindre un résultat probant permettant de rivaliser avec le procédé traditionnel en termes de qualité et de réduire le coût d’utilisation.