Simulation de production, modélisation dynamique et jumeau numérique
Ingénierie et Architecture
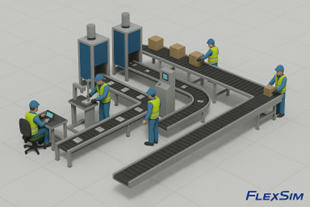
Ce projet de recherche appliquée porte sur la modélisation et simulation dynamique d’une ligne de production encore inexistante, commandée par un mandant industriel souhaitant optimiser ses futurs investissements. À l’aide de l’outil FlexSim, nous avons reconstruit virtuellement la ligne, en intégrant le layout prévu, les contraintes techniques spécifiques (système Kardex, convoyeurs, cuves de différentes capacités, niveau d’automatisation) ainsi que les paramètres humains (nombre d’opérateurs, organisation du travail).
L’approche vise à évaluer la performance future de cette ligne en fonction de la demande prévisionnelle identifiée, et à tester différents scénarios. L’objectif est de fournir au client une base décisionnelle robuste pour orienter ses choix d’investissement (CAPEX), tout en assurant une adaptabilité aux évolutions de la demande.
Les résultats ont permis de mettre en lumière les points critiques du système (bottlenecks, temps d’attente, saturation des ressources), et de simuler des ajustements progressifs (augmentation de la cadence, redimensionnement des buffers, ajout d’un poste de travail). Des indicateurs clés tels que le TRS, le throughput, ou la capacité résiduelle ont été analysés pour chaque scénario. Ce projet s’inscrit également dans un cadre plus large de recherche sur les jumeaux numériques adaptatifs. En intégrant les outils FlexSim et Tulip (MES reconfigurable). La simulation ne se limite plus à la conception, mais devient un outil de pilotage continu, en lien avec les flux d’information terrain. Une prochaine phase pourrait intégrer la simulation énergétique de la ligne pour dimensionner également les besoins et la consommation en énergie.
Ce cas illustre ainsi une démarche de production agile, modulaire et data-driven, en phase avec les enjeux de l’industrie 5.0. Il constitue un exemple concret de transfert technologique entre les avancées académiques en simulation et les besoins industriels en projection stratégique.