Improved damage detection of Pelton turbines through vibration-based methods
Ingénierie et Architecture
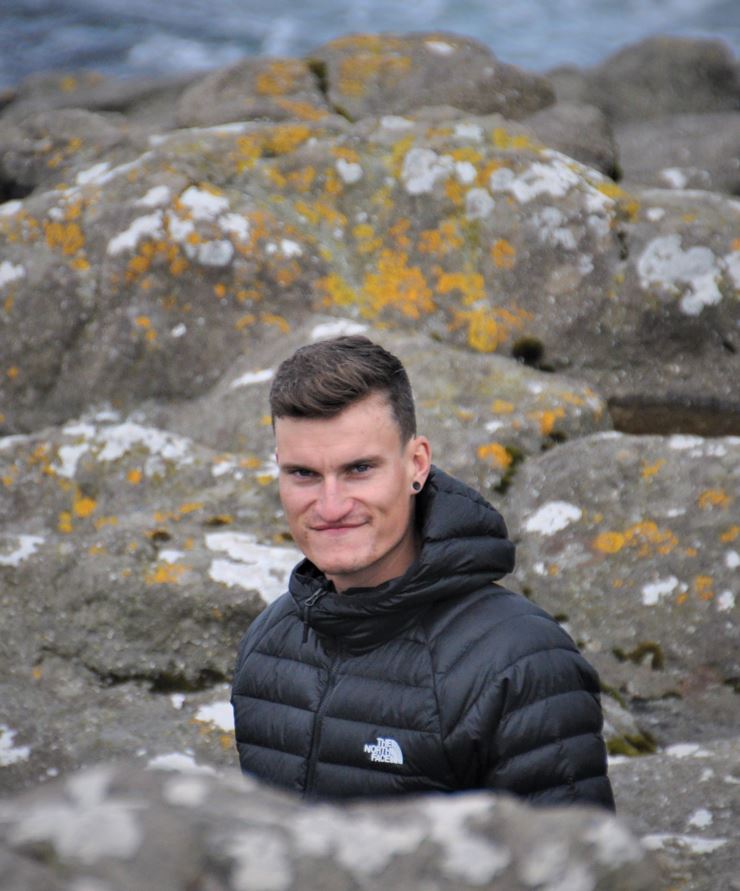
For a few decades, emerging new renewable energies have been influencing the electrical grid strongly and have been modifying the way hydroelectric power plants are operated. Thanks to their flexibility, hydraulic turbines are perfectly suited to compensate grid fluctuations. An increased flexibility implies more starts and stops experienced by the turbines which lead to broader fatigue cycles. For Pelton turbines, maximal stresses occur during start-up phases when the runner starts to rotate and the jet impinges the standstill buckets. Repeated cyclic loading might lead to fatigue cracks in the region of stress concentration. These cracks are very insidious as they could remain unnoticed for a while and suddenly propagate leading in the worst cases to bucket failure. Pelton turbines also suffer from hydro-abrasive erosion in particular in Alpine regions due to the large quantity of fine sediments contained in the water. For both cracks and hydro-abrasive erosion, visual inspections and non-destructive testing methods remain the only means of assessing the runner health state. These inspections are costly and require the turbine to stand still during the procedures, producing a loss of revenue for hydraulic power plant (HPP) owners, particularly during full load seasons. In the context of predictive maintenance, development of new monitoring tools to assess the remaining useful life of Pelton turbines is thus of primary importance to increase operating safety and reduce maintenance costs. The present project aims at deepening the understanding on Pelton turbine dynamic behaviour by conducting different experimental investigations on Pelton turbine prototypes. The results of this project could serve as a basis to develop new predictive maintenance tools for the monitoring of Pelton turbines.